The project aimed to design a manually operated assembly line for cylinder heads used in two-wheelers. The scope includes designing five stations with the required fixtures for tasks such as valve guide seal pressing, valve insertion, and the assembly of the spring seat and spring onto the cylinder head. A leak test machine will be added at the end of the line for final design validation.
Automotive Assembly Line
Cylinder Head Assembly Line
Our client, a renowned automotive supplier specialising in the commercial manufacturing of 2-wheelers in India, sought to enhance the production efficiency of their cylinder head assembly process. The end customer's product range includes engine components, cylinder heads, and frame parts for two-wheeler vehicles.
Scope
Challenge
The main challenge in this project was designing the pallet system. The pallet, which holds the product while resting on a conveyor, faced issues with pressing operations because pressing could damage the moving roller conveyor. This problem affected various stations, including the stem seal pressing, stem and valve press validation, valve seat leak testing, lock-off assembly, and the gravity return conveyor. Another challenge was ensuring that all these designs are completed efficiently and cost-effectively without damaging the components.
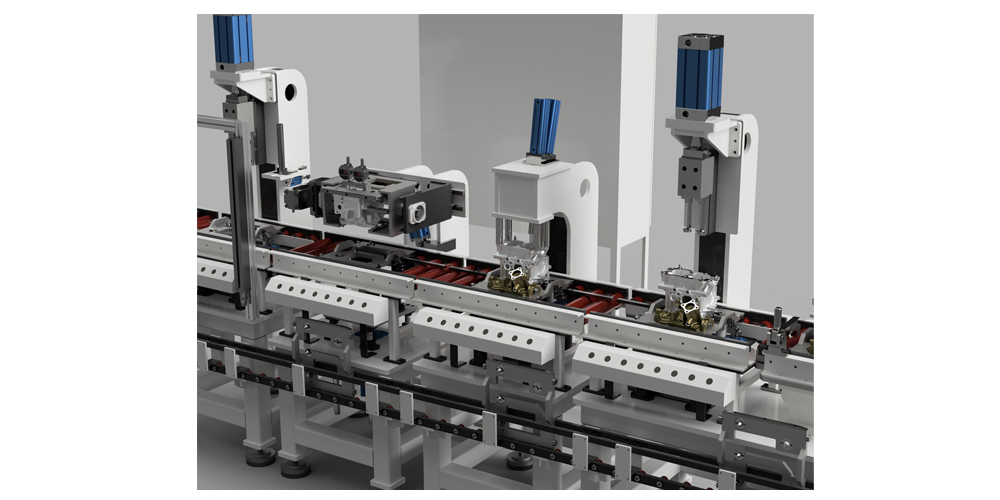
Solution
The assembly line design is divided into 5 stages or stations, with each stage operated manually. Pneumatic stopper cylinders are used between stages to halt the pallet, ensuring it stays in the correct position.
The first stage is the loading station. Here, the machined and cleaned cylinder head with cam cover is placed onto an empty pallet positioned on the loading station turntable. This station features a manual lock to secure the pallet and a lock pin to fix the turntable's rotation. The cam cover is removed using a designated tool and placed onto the pallet in its specific location. Plug holes are also sealed at this stage. The pallet is then moved to the pressing station.
The second stage is the stem seal pressing stage. Here, the pallet is halted by the stopper cylinder and raised by the lifter unit to detach it from the conveyor. The stem seal is then pressed using a pneumatically operated seal pressing tool. A safety light curtain is installed at the 1st and 2nd stations to prevent accidental interventions. The station is operated via electrical push buttons.
The third stage is the valve projection and checking station. At this stage, the cylinder head and cam cover are positioned, and the pallet is lifted and rotated 180° using an indexing mechanism. A digital indicator is used to verify the height of the inserted valve. This station is also controlled by electrical push buttons.
The fourth stage of the assembly line features a leak test machine that uses dry air at 1bar to check the valve seat area of the cylinder head for leaks.
In the fifth and final station, both inlet and outlet valves are pressed and secured using the valve lock tool. Once this process is completed, the pallet is moved to the unloading station, where the cam cover is reattached to the cylinder head and the assembly is unloaded. The empty pallet is then returned to the loading station via a gravity return conveyor.
All safety and ergonomic standards were adhered to according to the client's specifications. The proposed solutions incorporated thorough Design Failure Modes and Effects Analysis (DFMEA).
Value and Benefits
Sedin's cost-effective and innovative approach helps the clients to build and operate the machine smoothly and continuously, resulting in increased productivity.
The assembly line is designed with simplicity in mind, allowing for easy future expansions. This has significantly benefited the customer by reducing costs and boosting productivity. Our robust engineering expertise and commitment to quality have established us as a trusted and valuable design partner for the client.