To help our client develop multi-functional tillage machinery, we designed a versatile, high-performance system that could handle plowing, harrowing, and seedbed preparation with ease.
Our goal was to create a solution that reduces operational costs, minimizes labor dependency, and adapts to various land and farming requirements. The farm equipment design must be compatible with various tractor models and meet American, Australian, and European agricultural standards.
We categorized our solution into five key areas to ensure maximum efficiency and durability.
1. Research and Benchmarking Analysis
To ensure a high-quality agricultural machinery design, we conducted an in-depth benchmarking analysis in collaboration with the client’s R&D team. This involved:
- Evaluating existing tillage systems in the client’s product line to identify areas for enhancement.
- Analyzing competitor offerings to understand performance benchmarks and key differentiators.
- Assessing soil conditions and farming practices across different regions to ensure adaptability.
Based on these insights, we developed multiple product concepts, refining each for feasibility, cost-effectiveness, and alignment with customer requirements.
2. Material Selection
We developed three distinct variants of the tillage unit to meet the unique requirements of Australia, the U.S., and Europe.
To ensure durability and ease of manufacturing, we carefully selected materials based on availability and performance in each region:
Australia
We chose high-strength and wear-resistant materials based on the function of each part.
‣ Structural Components (Main Frame) – Used GR 250, GR 350, and Bisplate 400 for the main frame. These materials offer high durability, impact resistance, and structural stability while keeping the weight low.
‣ Machined Parts (Discs, Chains, & Linkages) – Chose 1045, 1040, 4140, and 20MnV9 for shafts, linkages, and pivot joints to ensure high strength, wear resistance, and smooth movement under tough conditions.
‣ Profile-Cut Members (Beams & Supports) – Used CL350L for rectangular and square hollow sections (RHS, SHS), providing strong yet easily fabricated support structures.
U.S. & Europe
We applied similar material selection strategies, choosing regionally available equivalents to match the performance of Australian materials while ensuring compliance with local regulations and supply chain efficiency.
3. Compliance with Global Standards
All designs adhered to Australian, European and U.S. industrial standards to ensure full compliance.
We followed AS 4100 for steel member design, AS 1170 for loading conditions, and safety regulations such as AS 2875-2000, AS 2153.1-2008, and ISO 12100.
Additionally, we ensured the designs complied with the EU Directive 167/2013 for equipment.
4. Detailed Design and Validation
We designed each variant to meet local agricultural standards, soil conditions, and tractor compatibility, ensuring reliable performance in the field. Our focus was on optimizing three key components that directly impact efficiency, durability, and ease of use: frame, discs, chains and linkages.
Once the design was finalized, we refined it using Design for Manufacturing and Assembly (DFMA) to make production efficient and cost-effective. To ensure long-term reliability, we conducted Design Failure Mode and Effects Analysis (DFMEA) to identify and eliminate potential weak points.
A detailed parametric model was created, followed by the development of manufacturing drawings, ensuring all documentation complied with relevant industrial and regional standards.
5. Data Management and Delivery
The finalized design files were stored in the client’s Product Data Management (PDM) system, enabling smooth collaboration across teams. Design changes and updates were efficiently handled within the PDM, ensuring controlled document versioning.
Our efficient product design approach helped the client reduce errors, minimize discrepancies and improve the accuracy of the final product.
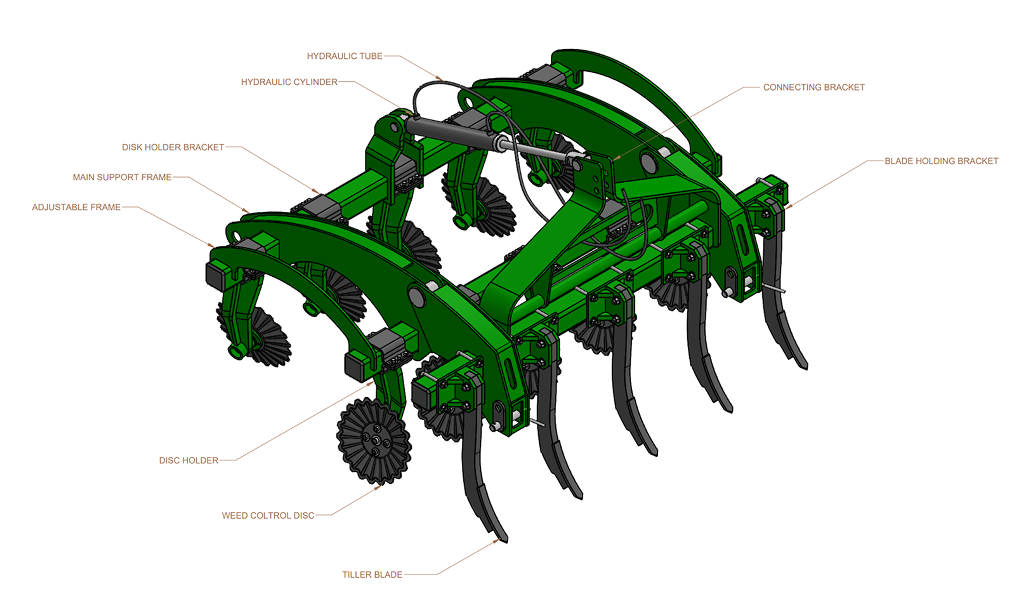