To address these challenges and meet the client’s requirements, we leveraged our design team’s efficient product design capabilities. We conducted thorough research into the latest technologies and design standards, working closely with the client’s engineering teams to understand their needs. Based on the input, we developed several concept designs that complied with international standards.
Our effective solution included:
Optimized Material Selection
As the initial step in our BESS container design process, we conducted thorough research and performed detailed load calculations to determine the right material and thickness. We selected high-strength, lightweight materials like high-tensile steel for the frame and corrugated panels.
To ensure the container could withstand the required loads while staying strong and lightweight, a 2mm wall thickness was chosen based on load analysis and material performance.
Detailed Design of the Container
- After selecting the material, we focused on identifying areas where we could reduce weight without compromising the container's strength. We designed a double-glazed wall system using thinner yet stronger steel sheets.
- We added precise ribbed patterns to the inner panel of the container to enhance rigidity and reduce weight. The outer panel was kept flat for protection. A specialized insulation layer between the panels provided thermal regulation and shock absorption, ensuring safety.
- We optimized the corner posts, cross members, and roof panels to balance strength and efficiency. The corner posts were reinforced to 4mm–6mm to withstand load stresses. This allowed us to reduce material in other areas without compromising durability. The bottom skid channels were also optimized for safer handling during transport and stacking.
- The design included efficient battery racks with secure mounting points and internal partitions to maximize space and improve organization. The internal layout of the container was optimized to ensure smooth operation. We strategically added access points for easy maintenance and quick access to key components.
- We added corner castings, mounting brackets, and internal structures to securely hold the battery components. The doors, frames, and handles were designed for both durability and visual appeal. Overall, the container design offered a modern, sleek look while ensuring ease of operation.
Static Structural Simulations
Once the container’s structure design was finalized, we used SolidWorks Simulation to test and validate its stability under static loads and impact during transport. The results confirmed the design could handle standard conditions without compromising integrity.
Thermal Management Design
To ensure optimal performance and safety of battery storage system, effective thermal management was a key consideration in the design. We integrated an efficient HVAC system into the container design by:
- Incorporating two AC chillers to cool the battery area, regulating the temperature inside the container.
- Installing two mounted fans on top of the transformer block to circulate the air and ensure efficient heat dissipation.
The design ensured that the temperature inside the container stayed within the required range, preventing excessive cooling or overheating. Additionally, we incorporated louver arrangement in the side walls and door to allow proper airflow, further preventing heat buildup inside the container.
Weather Resistance
An efficient weatherproof sealing was integrated into the design to protect the container from external environmental factors, ensuring long-term durability and safeguarding the internal systems.
All doors, joints, and access points were sealed with weather-resistant gaskets and sealants to prevent water entry.
We ensured the container complied with the IP54 Rating, ensuring protection against dust ingress and resistance to splashing water from all directions, especially during rains.
Compliance with Standards
We ensured the design adhered to ISO standards for shipping containers, specifically ISO 1496-1 for structural performance and ISO 668 for external dimensions. The design ensured the container can handle stacking loads up to 1.8 times its maximum gross weight, and its dimensions are accurate to meet functional requirements.
Final Design and Manufacturing Considerations
Leveraging our CAD expertise, we developed a 3D parametric model of the container to validate the design and ensure a precise fit for all components. We optimized the design for easy manufacturing by using standardized, globally available components, helping to lower material costs and reduce production lead times.
Our team also provided support to the client regarding fabrication techniques, including recommendations on where to use welded joints for strength and where mechanical fastening methods would be more efficient.
Our final deliverables to the client included a 3D model and assembly drawing of the battery energy storage system container.
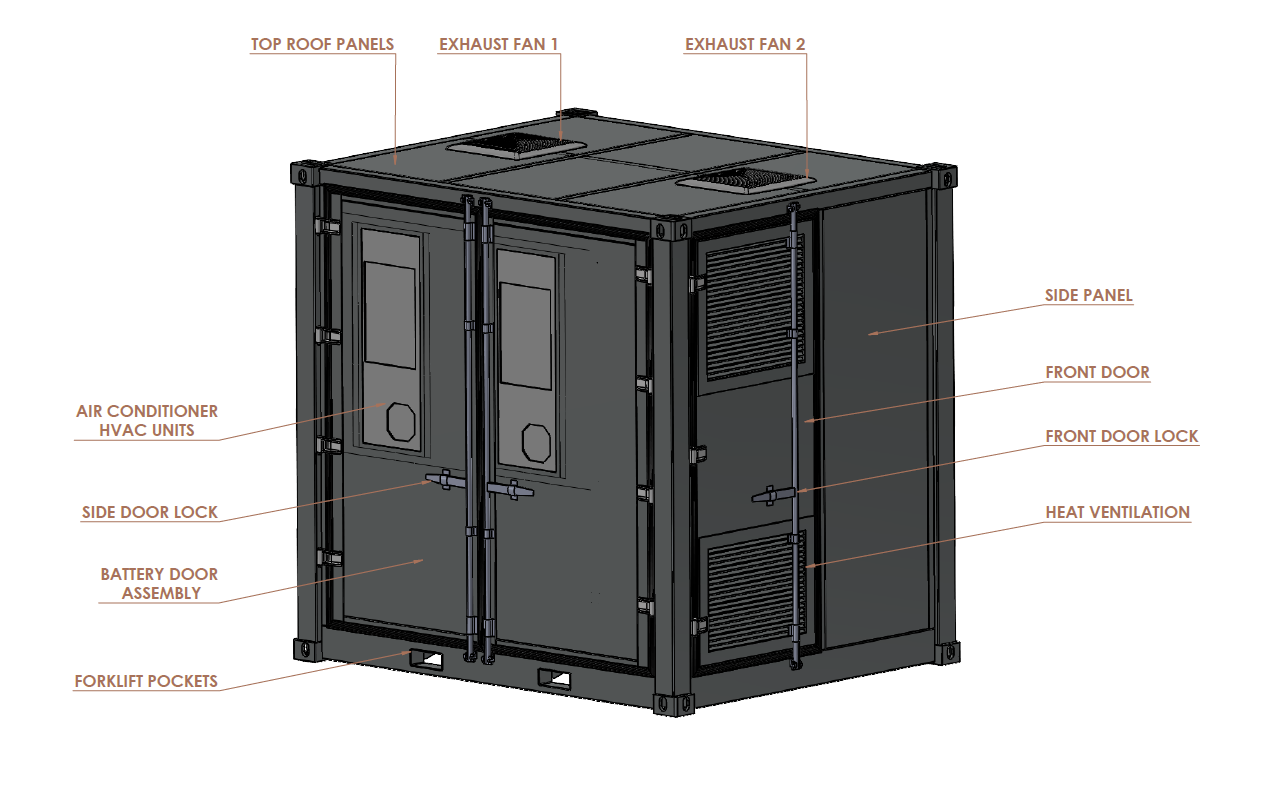