Leveraging our expertise in CAD conversion services, we systematically gathered all input data, categorizing them to develop an effective project plan. This structured approach helped us deliver high-quality outputs within the scheduled timeline, ensuring a smooth transition from 2D to 3D.
Here’s how we made it happen:
Accurate CAD Conversion
Using SolidWorks, we converted the 2D drawings into detailed 3D models, making sure every part was properly defined for manufacturing. To ensure accuracy, we:
- Refined bore tolerances, seal groove depths, and surface finishes to meet industry standards.
- Applied GD&T (Geometric Dimensioning & Tolerancing) for precise fits, ensuring proper assembly and function.
- Validated seal compatibility using supplier catalogs and engineering calculations to prevent leakage and performance failures.
Designing Complex Internal Components
The hydraulic cylinder contained intricate geometries and complex internal elements, such as pistons, seals, ports, and hydraulic chambers. All of these needed to fit and function perfectly. To get it done, we:
- Modeled each internal component separately and then assembled them to ensure everything worked together smoothly.
- Used advanced 3D modeling techniques to check how the parts would move in real-world conditions.
- Created section views and exploded models to double-check clearances and make sure everything fit as expected.
Design for Manufacturability
To ensure the hydraulic system was designed for easy to manufacture, we:
- Optimized deep grooves and sharp edges to make machining easier.
- We selected standard materials like ANSI 1045 steel, U400-15 cast iron, and ANSI 1040 steel to ensure the hydraulic cylinder is durable, strong, and cost-effective.
- We designed components to follow ISO standards, making manufacturing, maintenance, repairs, and future replacements easier.
Design Iteration & Quality Checks
Before finalizing the design, we went through multiple iterations, incorporating feedback from the client’s cross-functional team.
To ensure top quality, we conducted:
- FEA (Finite Element Analysis) in SolidWorks to validate durability and real-world performance.
- Tolerance analysis to prevent leaks, misalignment, or premature wear.
- Assembly checks to confirm proper fit and function.
Finally, thorough assembly and part drawings, including a comprehensive bill of materials (BOM), were generated to streamline the manufacturing process.
Sedin converted the legacy data into the required CAD format while ensuring compatibility with the client’s software. With a structured project plan and strict quality checks, we delivered accurate and ready-to-use files.
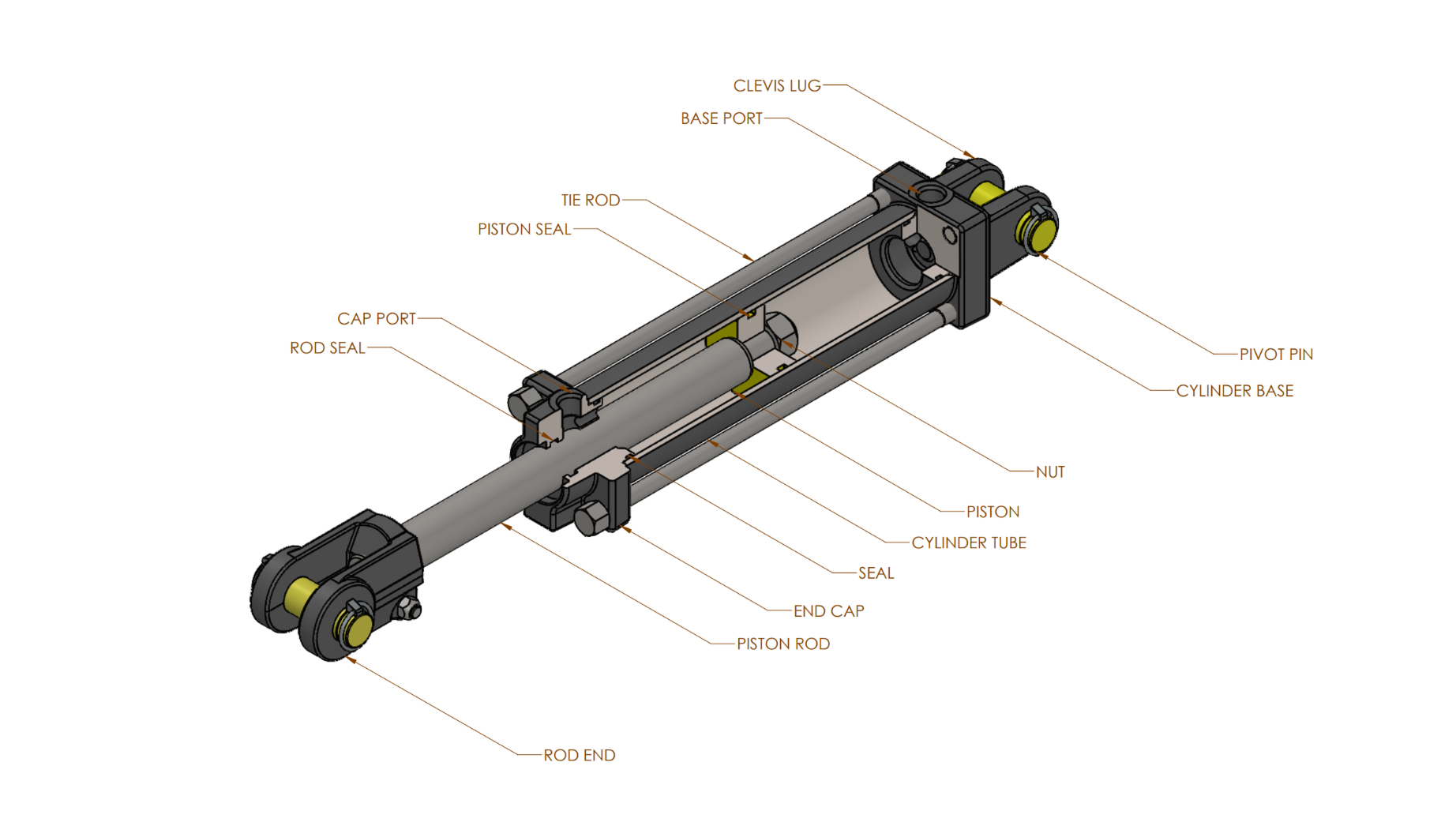