Leveraging our years of product design experience across diverse sectors, we created cost-effective and efficient solutions for the client. We conducted in-depth research on pediatric orthopedic implants, child anatomy, and biocompatible materials to ensure the best possible outcomes.
Our effective solution included:
Legacy Data Migration
With expertise in UG NX, our design team successfully converted the client’s legacy data into precise 3D CAD models. We ensured each model aligned with the latest design standards and manufacturing techniques.
We developed detailed 2D drafts and 3D models for the following products:
- Anatomic Low Profile Clavicle Plate (used for clavicle fractures to minimize soft tissue irritation)
- Clavicle Hook Plate (used for distal clavicle fractures that need stable fixation)
- Distal Clavicle Plate (stabilizes fractures in the distal clavicle)
- Growth Control Plating System (controls bone growth in pediatric patients for deformity correction)
- Malleolar 4.0mm Cannulated Screw Kits (stabilizes fractures in the malleolus of the ankle)
- Straight Fibula Plating System (fixes fibula fractures for stability and healing)
The designs incorporated biocompatible materials like Ti Grade 4 for the straight fibula and clavicle plates, Ti Grade 2 for the growth control plating system, and Stainless Steel 316 LVM for the screw kits.
Design Optimization
We designed the models to align with the client’s standards, ensuring smooth integration into their manufacturing process and easy system transfer. To enhance performance, we suggested improvements in plate contouring, screw hole placement, and mechanical integrity, making the implants more stable and effective for surgery.
We created 3D models for over 100 plates and screws in multiple sizes, ensuring a precise fit for different patient anatomies. This helped improve surgical precision, fixation strength, and overall clinical effectiveness.
Compliance with Standards
Our designs were optimized to meet the latest medical device standards, including FDA, ISO 13485 and ISO 10993 regulations. We also ensured the selected materials met relevant ASTM standards.
Throughout the process, we kept the client informed and incorporated their feedback, ensuring the final solutions met their needs for both functionality and manufacturability.
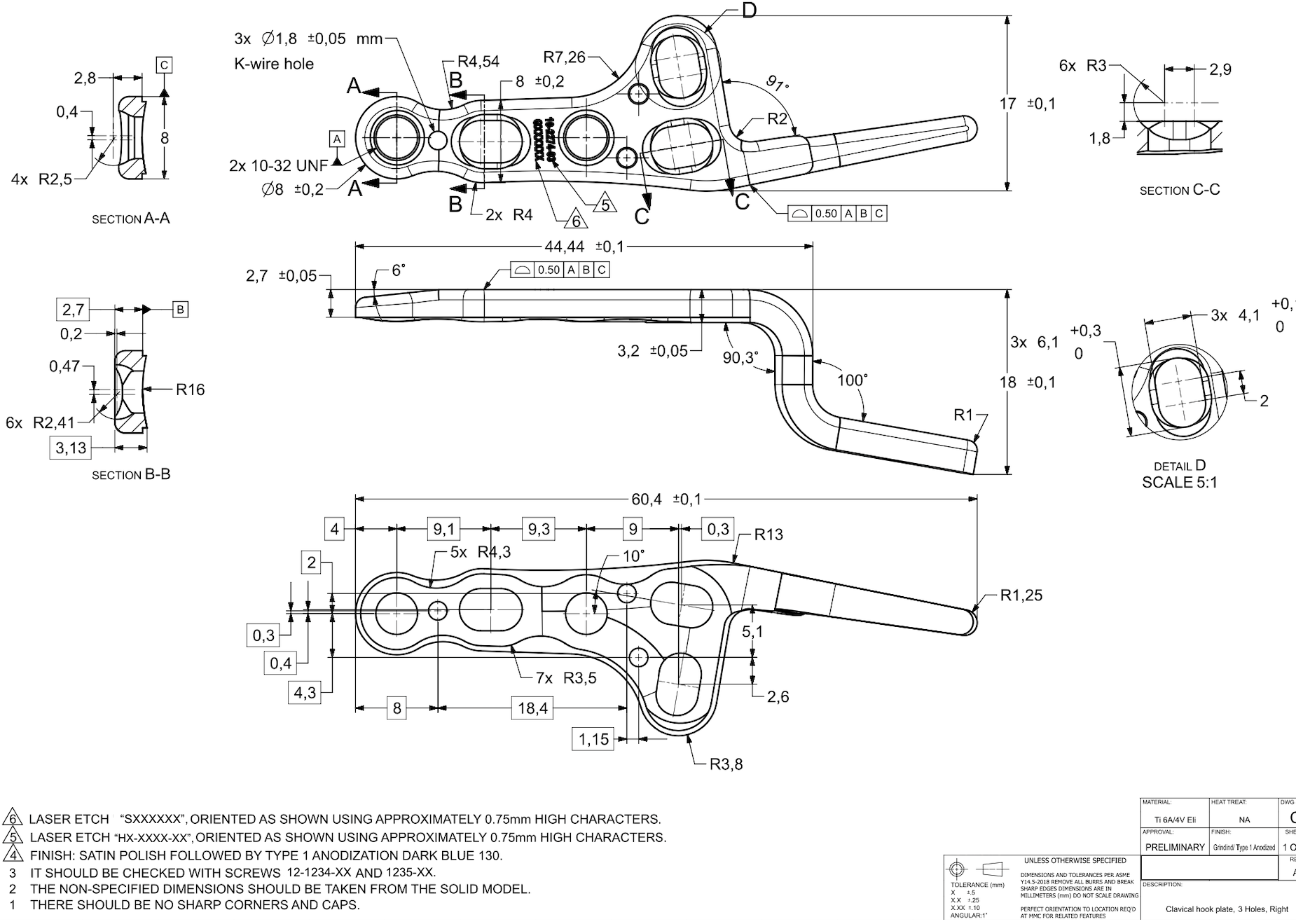