A state-of-the-art Pick and Place robot was designed with a payload capacity to handle various carton sizes. The robot was equipped with a gripper capable of adapting to different carton dimensions and weights. The EOAT was designed for easy adjustments, allowing quick changeovers between different carton sizes and all materials used in the EOAT comply with food industry hygiene standards.
A robust belt conveyor system was developed to transport cartons to and from the robotic pick-and-place station. The robot was integrated with an existing conveyor system to facilitate smooth and efficient carton case handling. The conveyor system was designed with adjustable heights, speeds and movements were synchronised to match with the robot’s operational pace and ensure smooth and continuous product flow.
Cognex Vision systems and through-beam sensors were implemented to detect carton positions, ensuring precise and coordinated operations. A user-friendly interface was developed for operators to easily manage and monitor the system, featuring quick changeover options for different carton sizes without the need for tools.
Safety barriers and emergency stop buttons were installed to protect operators and ensure compliance with safety regulations. The system was designed to minimise ergonomic strain on operators by automating repetitive tasks.
The automated system significantly boosted productivity, handling up to 100 cartons per minute. The robotic arm ensured consistent and precise carton handling, reducing errors and product damage. The system's flexibility to handle multiple carton sizes with quick changeovers increased operational efficiency, reduced labor costs and minimised downtime. Additionally, the automation improved safety and ergonomics by reducing the physical strain on workers.
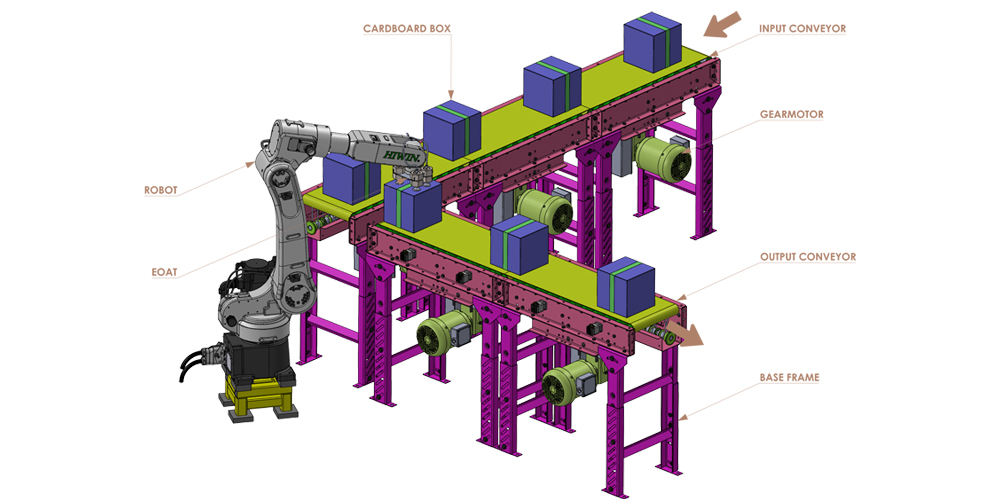