We were tasked with designing a Semi-Automated Servo U-Cap Pressing Machine for cylinder heads, featuring six U-Cap pressing stations. The machine needed to enhance production efficiency while adhering to strict quality standards, utilising three servo presses and one servo motor.
Special Purpose Machines
U-cap Servo Pressing Machine
Our customer, a Tier-1 supplier for major automotive companies, brings over 45 years of expertise in automated assembly systems. They offer comprehensive solutions in fixed, programmable, and flexible automation, including pressing and special-purpose machines.
Scope
Challenge
- Ensuring precise U-Cap placement and pressing from both top and sides without any component movement.
- Avoiding marks on components during manual loading and unloading.
- Reducing cycle time and increasing throughput without compromising quality.
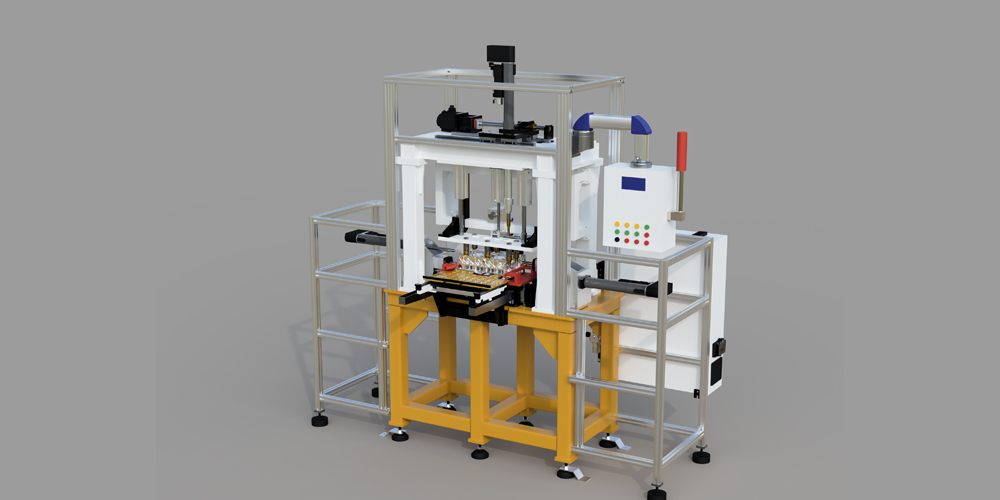
Solution
Our team designed a compact semi-automated machine with servo-actuated presses for accurate U-Cap application. Key features include:
- Dual Pressing Mechanism: U-Caps are pressed from both top and sides, with servo presses ensuring consistent force and depth.
- Operator-Friendly Design: Fixtures with foolproof setups and linear guides facilitate easy manual loading and unloading. Hydraulic cylinders provide precise component alignment during pressing.
- Advanced Control Systems: Real-time monitoring and adjustments ensure consistent quality. Comprehensive safety features, including emergency stops and protective enclosures, enhance operator safety.
Value and Benefits
The compact machine design lowered costs and boosted productivity. Precise servo presses ensured high-quality cylinder heads, with minimised cycle times and increased throughput meeting production targets. Enhanced safety and ergonomic features improved operator safety and reduced maintenance downtime, ensuring reliable performance.