The project involved designing and building an automatic ultrasonic welding cell for the rear step pad component, featuring two weld bosses. The solution needed to ensure precise alignment, accommodate various component geometries, and enhance welding efficiency, all while meeting stringent automotive and industry standards to boost production quality and efficiency.
Welding Automation
Ultrasonic Welding
Our customer, a Tier-1 supplier to a leading automotive manufacturer, specializes in advanced automatic solutions for complex plastic joining, finishing, and assembly applications. They offer a full range of services, including rapid prototyping and short production runs for plastic joining and assembly, with expertise in hot plate, infrared, and vibration welding, along with various plastic cutting and assembly techniques.
Scope
Challenge
The machine required three ultrasonic stacks and one generator, leveraging Herrmann’s next-generation welding technology. The limited space made integrating cooling sleeves and tubes challenging. The nesting process required non-marring materials, ergonomic considerations for component loading, and a compact machine design to save floor space. Welding the two intricate weld bosses consistently was crucial to maintain high-quality standards across large volumes, while the fixture had to be robust for continuous operation with minimal downtime.
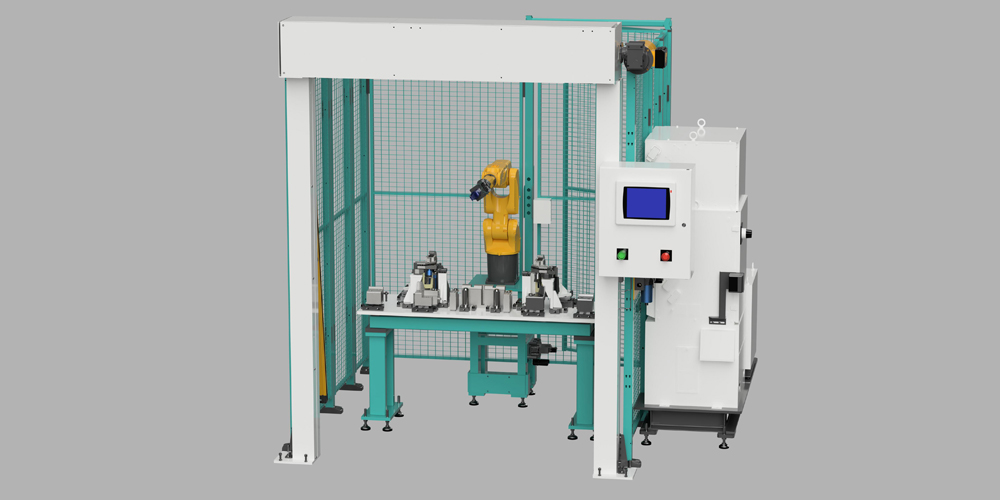
Solution
Our team developed a cutting-edge ultrasonic welding cell with a compact footprint, featuring a precise nesting and clamping system. The custom fixture was engineered to securely hold the rear step pad component, ensuring exact alignment of the weld bosses and accommodating slight geometric variations. The fixture utilised cylinders to secure the component, with locating and resting units on adjustable indexing cylinders for precise positioning in all three axes (X, Y, Z).
A customised End-of-Arm Tooling (EOAT) with a specialised titanium horn, designed to match the component profile, was mounted on a 6-axis robot programmed to accurately position the horn at specific weld points, ensuring consistent, high-quality welds. Ergonomic design principles were applied to reduce operator strain, featuring easily accessible clamps and controls, enhancing operator comfort and productivity.
The cell incorporated inline quality monitoring systems, providing immediate feedback to ensure each weld met required standards, with automatic rejection of non-conforming components. Safety measures, including barriers, light curtains, emergency stop buttons, safety interlocks on maintenance doors, and a shutter assembly, were implemented to protect operators and ensure compliance with safety regulations.
Value and Benefits
By integrating Herrmann’s advanced welding technology and a 6-axis robotic system, we delivered a high-precision and efficient welding solution. The adaptable fixture design supports future production changes, reducing the need for additional workstations and boosting overall efficiency. The ultrasonic weld cell significantly improved quality, throughput, and lead times, ensuring high-standard welds while enhancing safety and productivity. This project highlights our commitment to innovative, state-of-the-art solutions in automotive manufacturing, positioning our client for sustained future growth.