Design an arc welding fixture for 4 variants of rear axle. This fixture is manually adjusted for various variants. The fixture is to be flexible in nature as 4 more additional variants will be added as future scope. To design a welding fixture for the manual arc welding of rear axles, improving the accuracy, efficiency, and safety of the welding process.
Welding Automation
Welding Fixture
The End Customer are the pioneers and tier-1 suppliers for the manufacturing of various automotive products ranging from axles, suspensions, clutches, brakes etc. The Customer provides various automated and manual equipment to the End Customer. The existing manual welding process was inconsistent, leading to variability in weld quality and increased production times. They sought a solution that would enhance precision, reduce cycle time, and ensure operator safety.
Scope
Challenge
Design the fixture to accommodate multiple variants of the rear axle with complex shapes and sizes. The primary challenge was managing the diverse sizes and geometries of the rear axle, including current variants and four additional future variants. Each variant has unique dimensions and shapes. The welding fixture must ensure Improved weld quality, high accuracy, efficiency, and safety throughout the welding process.
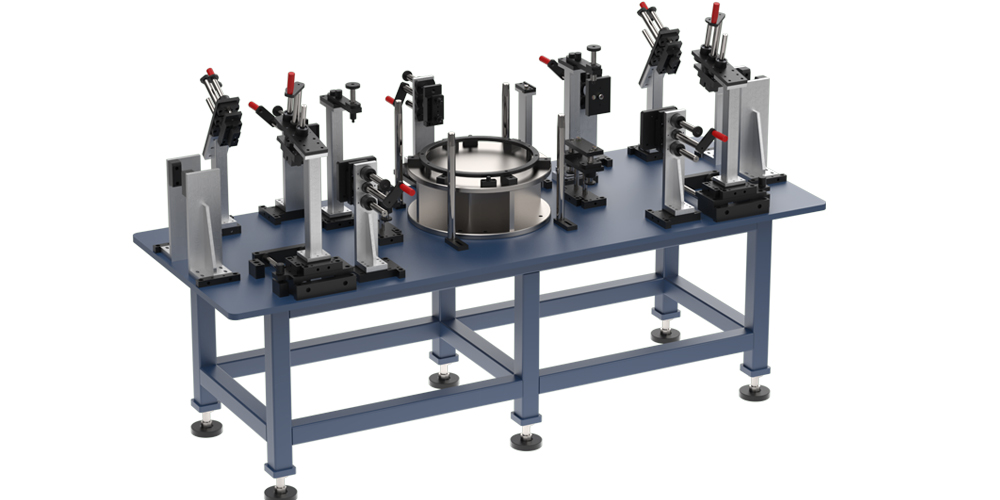
Solution
- A detailed study of the rear axle data was conducted before designing the welding fixture to understand the complexity of the component’s size and geometry and current production challenges. The fixture featured a central common locating and resting unit to hold the rear axle securely.
- The fixture includes resting and clamping units on either side to accommodate various rear axle variants. Clamping mechanism were designed to securely held the rear axle in place, ensuring stability during welding. These units are manually adjustable based on the specific axle variant, with each position catering to a particular part. The fixture is designed for quick changeovers or variant adjustments, minimising setup time. Additionally, necessary guide units are provided where possible.
- While designing the fixture, ergonomic principles were incorporated to reduce operator strain, such as easy-to-reach clamps, controls, quick loading and unloading. We also ensured the fixture's durability by using heat-resistant materials to withstand the high temperatures of arc welding. Additionally, the fixture was designed to accommodate future component variants.
- Since this is a manual arc weld fixture, all resting and clamping units and pads were coated with hard chrome plating to resist spatter accumulation in the welding areas. Additionally, some parts of the clamping and resting units were made with copper due to its beneficial material properties. All safety, ergonomic, and welding standards, along with the end client's specifications, have been incorporated.
- The new welding fixture significantly improved weld quality by ensuring consistent clamping, which enhanced the strength and durability of rear axles. Safety features greatly reduced the risk of accidents and injuries. The fixture also increased production efficiency by cutting down welding cycle times and eliminating bottlenecks. Its adjustable design allowed for quick adaptation to different rear axle models, making it versatile and future-proof.
Value and Benefits
With extensive experience in weld cell building, Sedin delivered the manual arc welding fixture on time, ensuring high quality and helping the customer meet their market schedule. The fixture's versatility and futuristic design saved the customer a significant amount. The successful implementation of this welding fixture for rear axle arc manual welding demonstrates our commitment to innovative and effective solutions in automotive manufacturing. Our strong engineering skills and quality standards made us a trusted and valuable design partner.