The goal of this project was to design and implement a custom EOAT capable of safely and efficiently handling glass panels and tailgates. The EOAT needed to be capable of transferring the tailgate between Bonding station, Inspection station and finally to curing conveyor. EOAT should accommodate the weights of glass and tailgates while ensuring precise placement and minimising the risk of damage.
Material Handling
EOAT
The customer has over 40 years of experience in designing and manufacturing a variety of specialised machines and equipment. They are experts in creating fully integrated assembly machines, stand-alone machines, various welding cells, and automated systems including Glass and tailgate. Their expertise includes custom automation assembly systems such as fixed, programmable, and flexible automation, as well as ultrasonic welding and support services.
Scope
Challenge
- The EOAT must securely hold the tailgate with the glass assembled, maintaining a firm grip on all sides throughout the operation without any deviations.
- The payload of the EOAT, including the Factor of Safety (FOS), should not exceed 75kg.
- Handling the fragile glass panels safely is crucial to prevent scratches, cracks, or breaks.
- The EOAT needs precise positioning capabilities to ensure the correct placement and alignment of the glass and tailgate, providing the necessary degrees of freedom.
- Ensuring operator safety and ergonomic operation is of utmost importance.
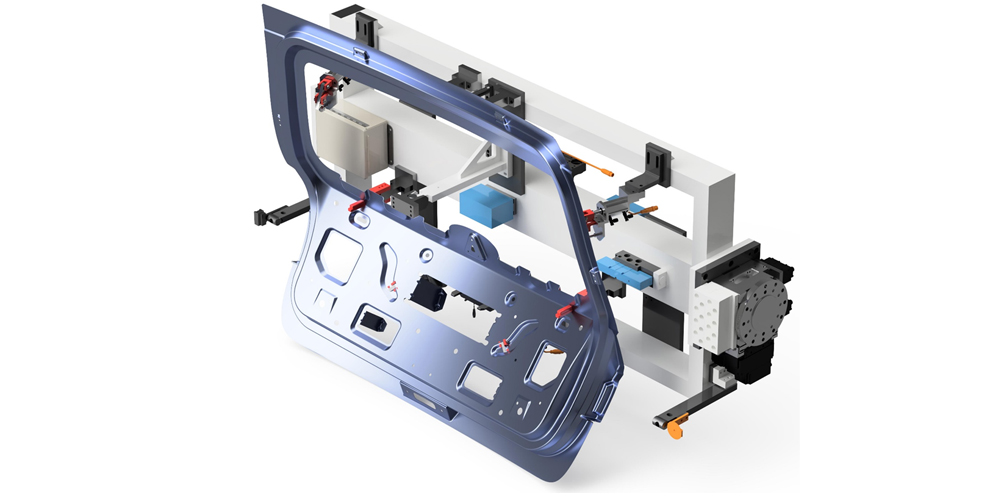
Solution
Our engineering team designed a state-of-the-art EOAT to fulfill the project scope. We have created a compact and efficient design to tackle the challenges effectively.
- Nylon material was used for all rest pads in the EOAT design to prevent any scratch marks or cracks on the glass surface.
- Two vacuum suction cups are incorporated to ensure a secure grip on the glass and tailgate, with their arrangement designed to evenly distribute the tailgate's weight. Additionally, three clamp units are provided, and the tailgate has approximate alignment guidelines.
- The EOAT features a central nest block that serves as the component's locating and resting point, along with two up/down locators to assist in positioning and docking the EOAT at the next workstation in the line.
- The presence of a product (glass and tailgate) is detected using a distance sensor. The data carrier, which holds machine-readable information, and the ATI coupler, fixed to the robot, provide signals that enable the EOAT to perform its operation.
All safety and ergonomic standards were adhered to according to the client’s requirements. The solutions were developed with careful consideration of DFMEA (Design Failure Modes and Effects Analysis) and payload validation.
Value and Benefits
The custom EOAT for handling glass and tailgates delivered outstanding results, exceeding client expectations. It significantly improved cost efficiency, productivity, and product quality while ensuring a safe and ergonomic workspace. Our engineering expertise and high standards established us as a trusted design partner. The new EOAT enhanced the production line, increasing speed and reducing cycle times by 20%. Its precise grippers and control mechanisms minimised the risk of damage to glass panels and tailgates.