Our team developed an advanced pressing machine that met the project’s requirements and addressed its challenges effectively.
The machine features two distinct fixtures for shaft and spline yoke assembly, mounted on a sliding unit with an electrical slide. Adjustable clamping units secure components during the greasing and assembly process. The operator manually loads components into the fixtures.
A bridge assembly, including a crimping tool with LVDT and a pick-and-place mechanism, accommodates varying shaft lengths. An HMI, electrical slide, pneumatic cylinders, FRL, sensors, safety light curtains, grease pump, and printer control various functions as needed.
The spline yoke is placed in a grease filling station fixture, where an automatic grease pump applies the precise amount of grease, ensuring consistency and preventing over- or under-greasing. After greasing, the yoke is unloaded and placed into the assembly fixture, where an automated mechanism handles parts gently to prevent damage or misalignment.
The assembly cycle begins with the operator pressing the Cycle-Start button. The shaft assembly moves towards the slip yoke with the required force and distance. Pincer units, equipped to move vertically and horizontally, align with the boot clamp and spline bar assemblies. An LVDT linear scale verifies and maintains positioning.
The machine ensures proper boot positioning before crimping boot clamps with a force of 4000N ± 200N. Pneumatic cylinders manage automatic unloading, distributing assembled components onto a conveyor. The system’s design allows easy integration and future fixture upgrades.
Real-time monitoring with sensors ensures each part meets quality standards, with deviations detected and corrected or rejected promptly. Safety and ergonomic standards were meticulously followed, and all aspects of DFMEA (Design Failure Modes and Effects Analysis) were considered. The cost-effective design enabled continuous operation, boosting productivity.
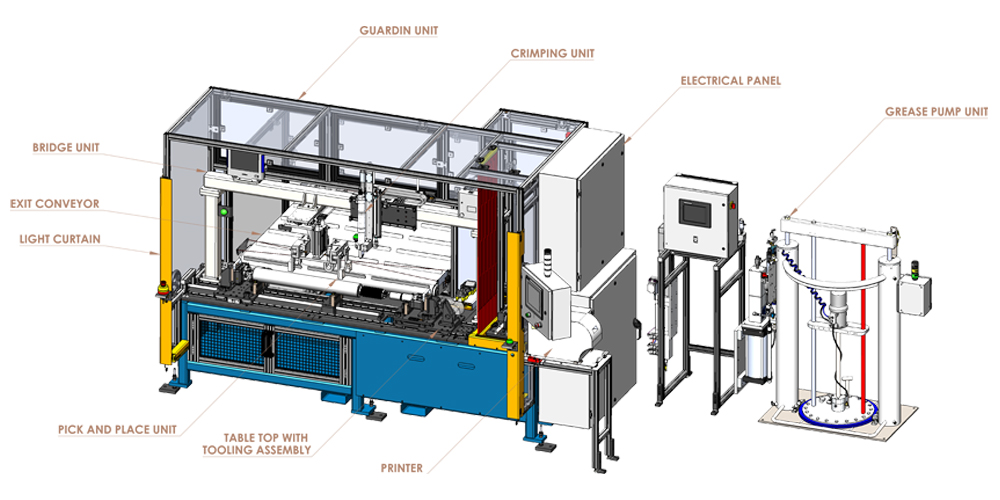