The scope of this project was to design a Semi automated machine for assembling radiator cores of five different sizes, with interchangeable setup units as needed. The primary function of the machine is to collect and assemble radiator elements for IC engines and press them together to form a complete radiator within a cycle time of 120 seconds per component.
Automotive Assembly Line
Radiator Assembly
The project was completed for a well-known automotive supplier specializing in manufacturing and commercialization. The end customer's products ranges from radiators, bumpers, tailgates, spoilers, and car body panels.
Scope
Challenge
- Designing a single holding fixture to accommodate five variants and multiple sizes of radiator elements, including tubes, fins, headers, and end plates.
- Securely handling and performing the pressing operation of the radiator components.
- Meeting the available cycle time of 120 seconds per component.
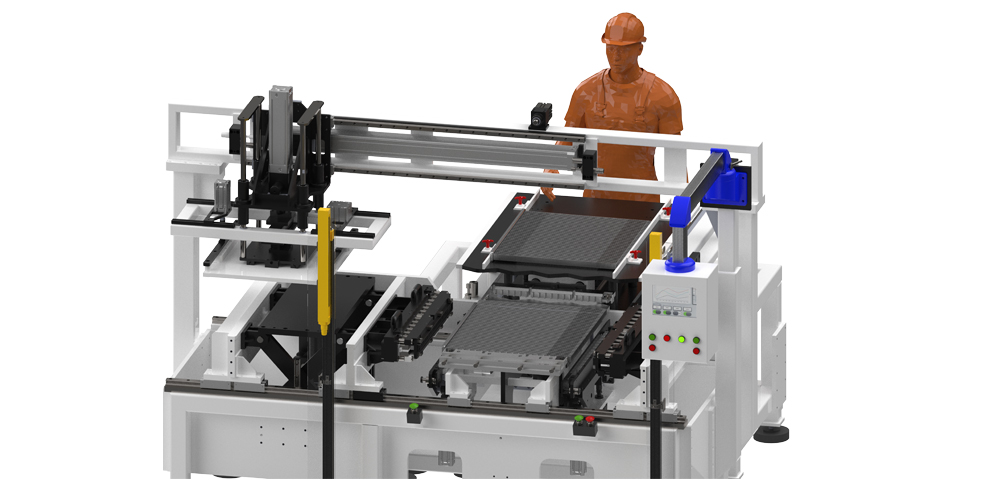
Solution
- To achieve the cycle time for 5 variants, common holding fixtures are designed and mounted on a slider unit with changeover capability.
- Two operators are planned for the entire assembly process to perform loading and unloading operations.
- One operator will load End Plates and Header RH & LH on side A of the machine, while the other operator will load all Fins and Tubes on side B.
- The components on side B will be clamped by the core operated assembly and then slide towards side A using a servo-operated gantry system.
- The clamping unit will secure the components from the top and move with the help of a slider unit powered by a rod-less cylinder.
- Using a scissor mechanism, Headers are pressed towards the Tubes, and from the other direction, End Plates are positioned using a servo motor.
- Once all the components are interlocked, the operator on side A will place a holding unit in the designated location in the nest and lift the component. The component will then proceed to brazing and final operations outside the machine.
Value and Benefits
By simplifying the changeover type unit and standardizing most of the components for all variants, reduces the cost of purchasing multiple machines for different variants or sizes. The cycle time has been reduced considerably and machine could run easily for 5 variants without any hustle.