The customer's goal was to design a versatile robotic drill cell capable of accommodating all variants of sleeper roof caps, which included three different sizes. The entire drilling process needed to be completed within a cycle time of 7.5 minutes per part.
Automotive Assembly Line
Robotic Drill Cell
The customer is a USA-based, esteemed supplier to renowned truck manufacturers. They have a broad market presence in various regions, including the USA, Europe, and Australia.
Scope
Challenge
- Designing a robotic drill cell capable of handling multiple variants of sleeper roof caps, with sizes of 80”, 72”, and 58”.
- Completing the drilling process using Suhner drill units and two robots within a cycle time of 7.5 minutes per part.
- Drilling up to 112 holes for the largest sleeper roof variant.
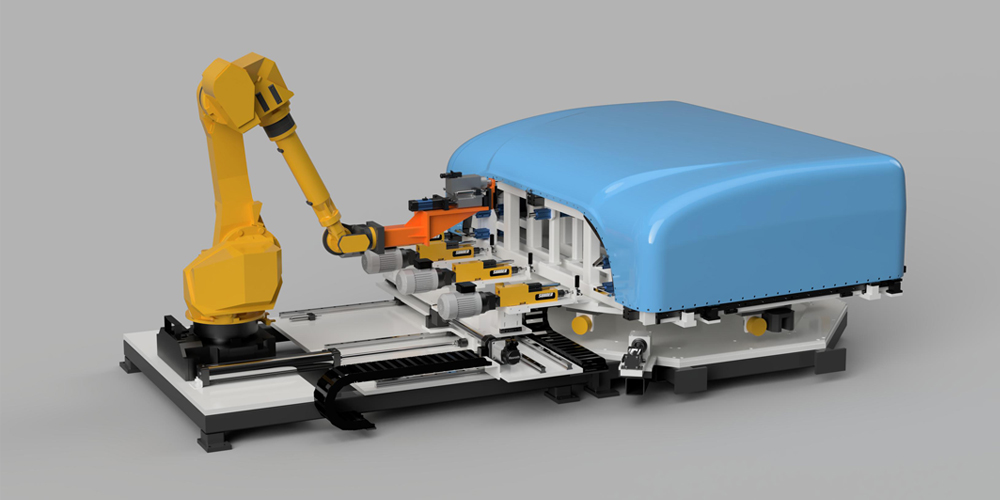
Solution
Meeting the required cycle time posed a challenge, so we implemented the following plan to achieve it:
- Develop fixtures for the various sleeper roof cap variants.
- Design a turntable to accommodate multiple fixture variants.
- Divide the drilling process into two stages: Section A and Section B.
- Accommodate a drilling waste collection unit into the design.
- Incorporate safety measures and failure mode analysis throughout the design process.
We designed three distinct fixtures to accommodate 80", 72", and 58" sleeper roofs. Each fixture uses a nest block and vacuum cups to ensure contact with all faces of the sleeper roof. The turntable allows the work-holding fixture to be positioned at the optimal angle and orientation, ensuring accurate and efficient drilling. Additionally, a dedicated fixture is designed for each sleeper roof variant to securely hold the workpiece in the correct position during the drilling process, which is crucial for achieving precise results.
To achieve the desired drilling cycle time, we have added two additional drill assemblies to the existing setup. One assembly includes four Suhner drill units and a robot with a drilling end-of-arm tool (EOAT), while the other features two Suhner drill units and a robot with a drilling EOAT.
These assemblies handle drilling the rear and side holes of the sleeper roof and can index in both X and Y directions for precise and accurate drilling. Corner holes are drilled using a robot. We have also made several modifications to the Sequence of Process (SOP) to enhance safety and ease of operation, resulting in reduced lead times and a safer working environment.
Sedin has performed initial level engineering analysis to ensure that the proposed designs adhere to the industry standards and meet customer requirements. All Design Failure Modes and Effects Analysis (DFMEA) have been taken into consideration and incorporated into the solution proposals. By integrating additional drill units alongside the robot drills, we successfully met the desired cycle time for the entire system, ensuring smooth and efficient drilling operations.
Value and Benefits
By adding multiple drill units to the robot drills, we achieved the required cycle time for the entire system, allowing for smooth and efficient drilling operations.
This approach ensures that the drilling process is completed within the desired timeframe, which is crucial for meeting production goals and ensuring customer satisfaction.
By having Sedin engineers develop the concept design, our client significantly reduced design costs and achieved the project ahead of schedule. The solution crafted by Sedin engineers is both cost-effective and easy to manufacture.