Leveraging our expertise in industrial automation and PLC programming, we created an efficient solution for our client’s cylinder head assembly line. The goal was to improve efficiency, reduce errors, and ensure high product quality.
We categorized our solution in seven key steps:
1. Identify key needs and customize the approach
We analyzed the cylinder head assembly line’s workflow and understood the challenges. As each station had specific tasks, we designed a flexible, efficient solution to integrate with the existing setup.
2. Create custom PLC logic
We developed custom PLC programming using Siemens’ SIMATIC STEP7 software to synchronize all five stations, sequencing operations to ensure smooth workflow and avoid conflicts.
The program included interlocks to prevent the next station from starting until the previous one had completed its task. Pneumatic stopper cylinders were controlled by the PLC to ensure precise stopping and positioning of pallets at each station. The PLC logic managed any discrepancies.
3. Develop user-friendly HMI for real-time control
Our controls engineers used Siemens’ WinCC to design an efficient HMI that provided intuitive controls for operators, allowing them to easily switch between manual and automated modes. This flexibility was crucial for tasks requiring human intervention.
The PLC logic also made sure manual actions didn’t disrupt the overall sequence. Real-time data on cycle times, part counts, and error alerts were displayed for operator efficiency.
4. Pallet Positioning and Valve Height Validation
We integrated a digital indicator at the valve projection and checking station, allowing the PLC to validate the height of inserted valves. The HMI displayed results. Any deviations from the expected results prompted corrective actions.
Our PLC program also ensured accurate pallet positioning at each station, helping reduce alignment errors and keep the assembly process consistent.
5. Ensuring safety and comfort
We integrated safety light curtains into the PLC program for the first and second stations. This measure would halt operations if obstructions were detected. Moreover, the HMI allowed operators to monitor safety conditions and immediately respond to any breaches.
Emergency stop buttons and safety interlocks were programmed and tested to meet client requirements. All safety features were integrated in compliance with IEC 62061 to ensure the highest level of protection. We also prioritized ergonomic controls to reduce operator strain.
6. Leak Test for Final Quality Assurance
The leak test machine was integrated into the PLC program for automatic validation of the valve seat area. The system ensured that the test results were within acceptable parameters before advancing to the next stage. Data from the leak test was displayed on the HMI, ensuring real-time quality control.
7. Rigorous Testing and Deployment
We conducted extensive testing to validate the entire system, ensuring the PLC and HMI worked as intended. Strict adherence to programming standards like IEC 61131-3 was maintained throughout the process.
We also performed simulations to fine-tune the final solution. After successful testing, the system was deployed with full support during the initial runs.
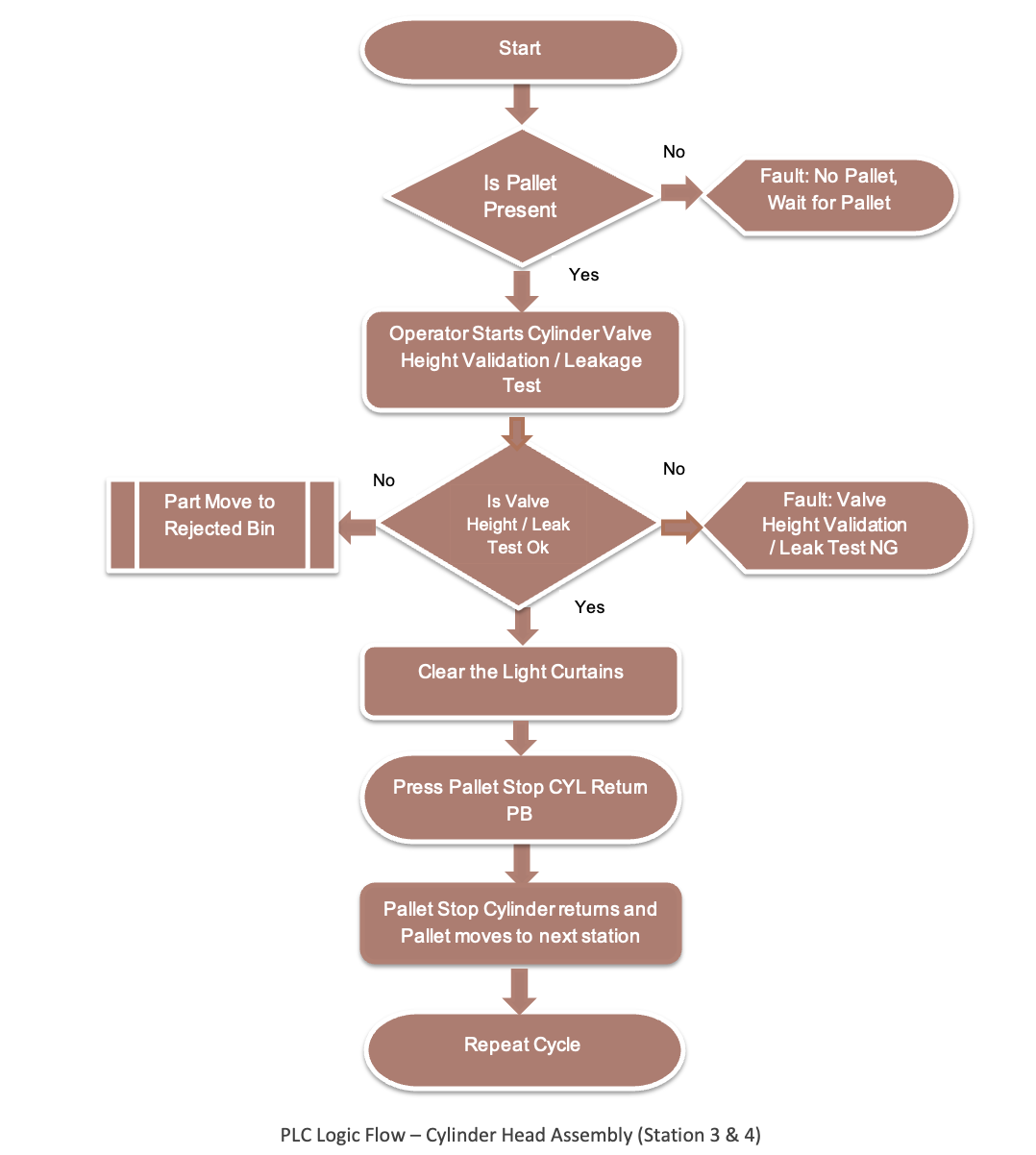